“IT’S A SMALL STEP FOR A MAN… ONE GIANT LEAP FOR MANKIND”
And BOPP played an active role in this achievement!
On 20 July 1969, some 600 million people watched as Neil Armstrong and a little while later his colleague Edwin Aldrin first set foot on the dusty surface of the moon, while Michael Collins, the third Apollo 11 astronaut, steered the mother ship in orbit round the moon. The driver behind this utopian project was competition between the superpowers of the USA and the Soviet Union to achieve the top spot in high technology. By 1957, the Soviet Union had already put the unmanned satellite Sputnik 1 into orbit around the earth, and just four years later Russian Juri Gagarin became the first man to orbit the earth. The obvious technological advantage taken by the Russians prompted American president John F Kennedy to make a corresponding challenge. On 25 May 1961 he stated before Congress his goal to land a man on the moon within that same decade, and to bring him home again. Before the end of that same year, NASA engineers had identified 10,000 different problems which needed solutions. 400,000 people and 20,000 businesses and institutions took part in the project. Given the uncertainly of commercial success, the budget of 25 billion dollars demonstrates just how much determination lay behind the project

Time was tight and the technological challenges were significant. There was a real lack of high performance rockets and experience in manned space flight. Development of the Saturn rocket series and 21 manned space flights in the shape of the Mercury, Gemini and five Apollo missions laid the groundwork for Apollo 11 to land on the moon. By December 1972, five further moon landings had been completed, with increasingly longer stays on the surface. For the last three Apollo missions - 15, 16 and 17 - a moon rover was used which enabled fact finding tours up to six kilometres away from the landing site. During the six missions, in total 382 kilos of stones and sand were collected.
From a technical point of view, all the businesses inolved were faced with significant challenges, as in most areas this was all totally new territory. Intense competition developed between developers and manufacturers, and also between filter and steel mesh producers. The demands in terms of specification, quality and delivery deadlines were enormously high, and cooperation between partnering businesses with no prior involvement had to work seamlessly from the start. We developed and produced various fine meshes in specifications from 80 x 700 up to 325 x 2300 especially for this project. For Wolfhalden, only opened a few years earlier in 1956, this represented a massive challenge, which began with sourcing fine wires up to 25 microns. It was exceptionally difficult to source these materials, or weavable wires. Weaving was still carried out on shuttle looms, which presented additional challenges for the already fragile wires.
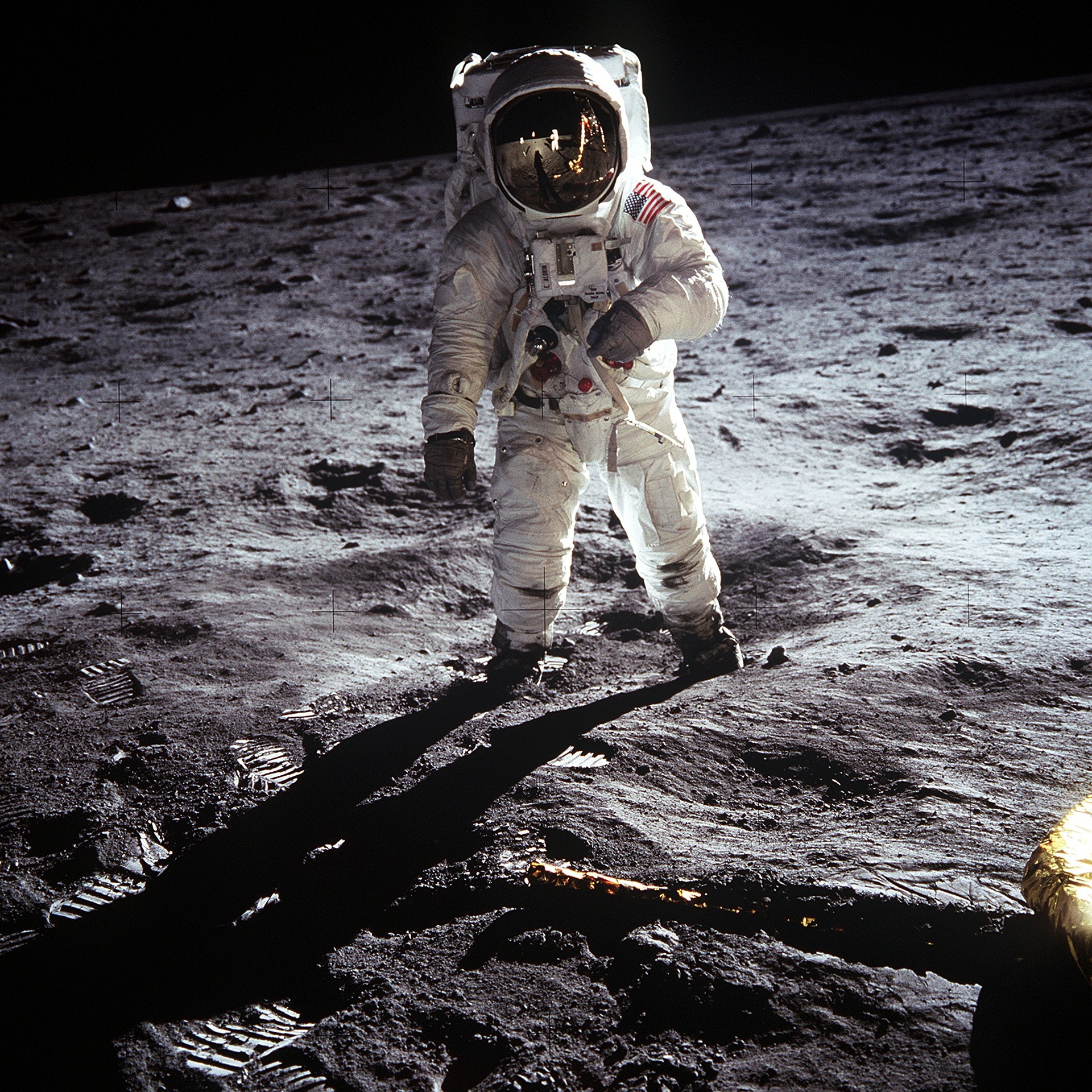
At the time, the customer for our meshes was Wintec Corporation, based in California, a specialist in the manufacture of filters and a certified supplier to NASA. Our meshes were initially used in around 80 different filter modules. Every Saturn V/Apollo flight was equipped with 760 filters. For the Apollo ship itself there were fuel filters for the response control system drives, filters for the helium, pressure, regulating and check valves, pneumatic filters for the drive systems, waste disposal filters, filters for oxygen ventilation, water filters for the environmental control system and rapid separation filters. The Saturn V rockets used the meshes in engine filters for fuel and control valves, cardan shaft drive filters, filters for liquid oxygen and pneumatic systems, regulation and hydraulic pump filters in the main drives. Our meshes were even used in the launch gantries, to supply fuel to the three drive systems of the space ship sections
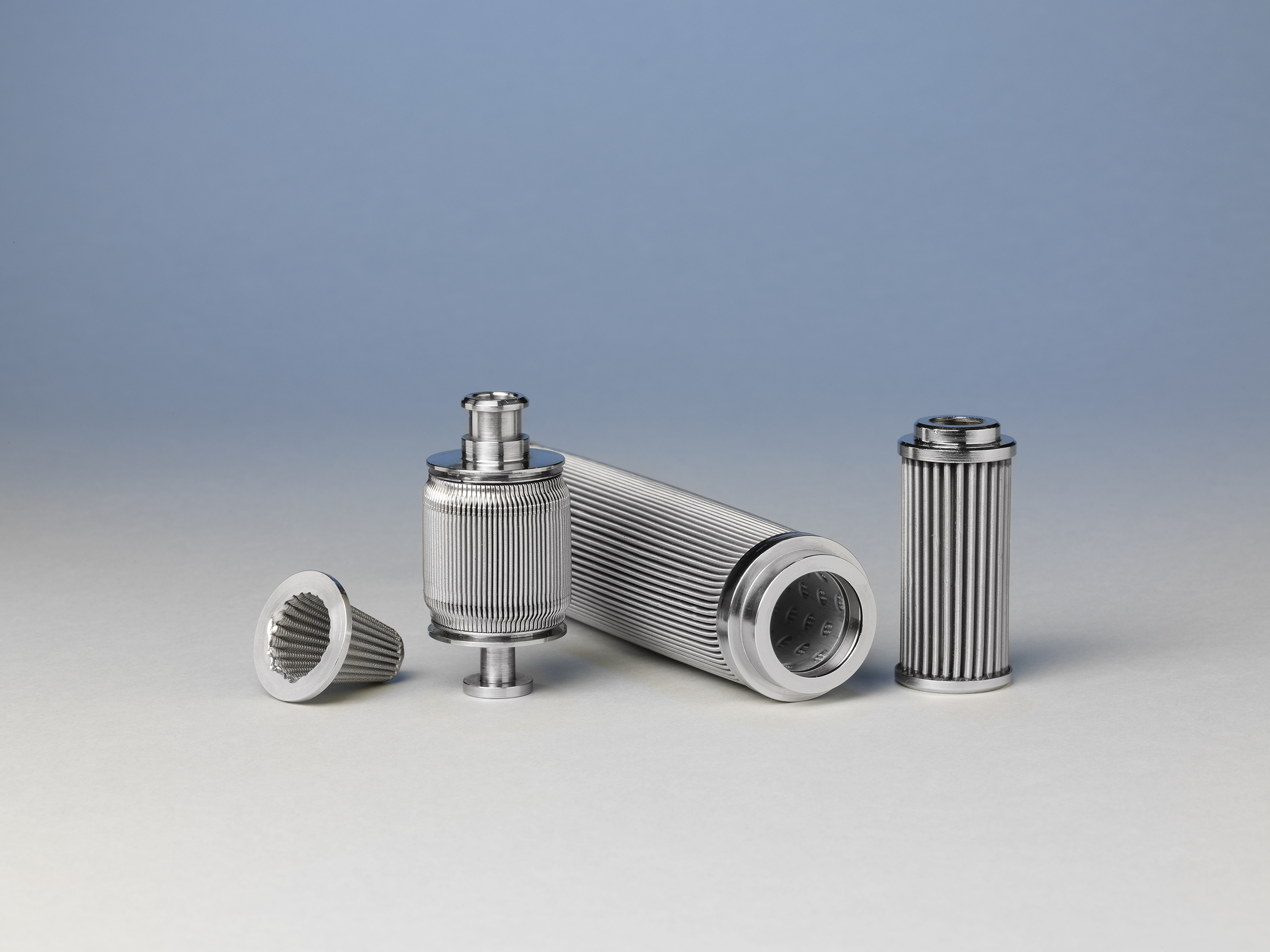
Cooperation with NASA and Wintec was complex, not just because of the geographical distances involved. Protoypes often had to be reworked following initial tests, to extremely tight time schedules. Close contact at the highest technical level between different levels of management and organisation – the later space shuttle programme also relied upon BOPP meshes – gave our business not just significant prestige but also a step change in experience, which in subsequent years has often facilitated breakthroughs in challenging application areas and development projects.
During the space travel programme, BOPP gained a wealth of knowledge in the weaving of fine wire. Countless test methods and trials developed and carried out by our customers and other institutions now serve us well in terms of application technology. We demonstrated that the BOPP team was capable of achieving the exceptional, and that we play in the premier league. The same holds true today. We have colleagues who excel in their roles, and we have state of the art plant, equipment and infrastuctures. Our strengths lie in innovative thought, professional working processes and premium quality across our product range.
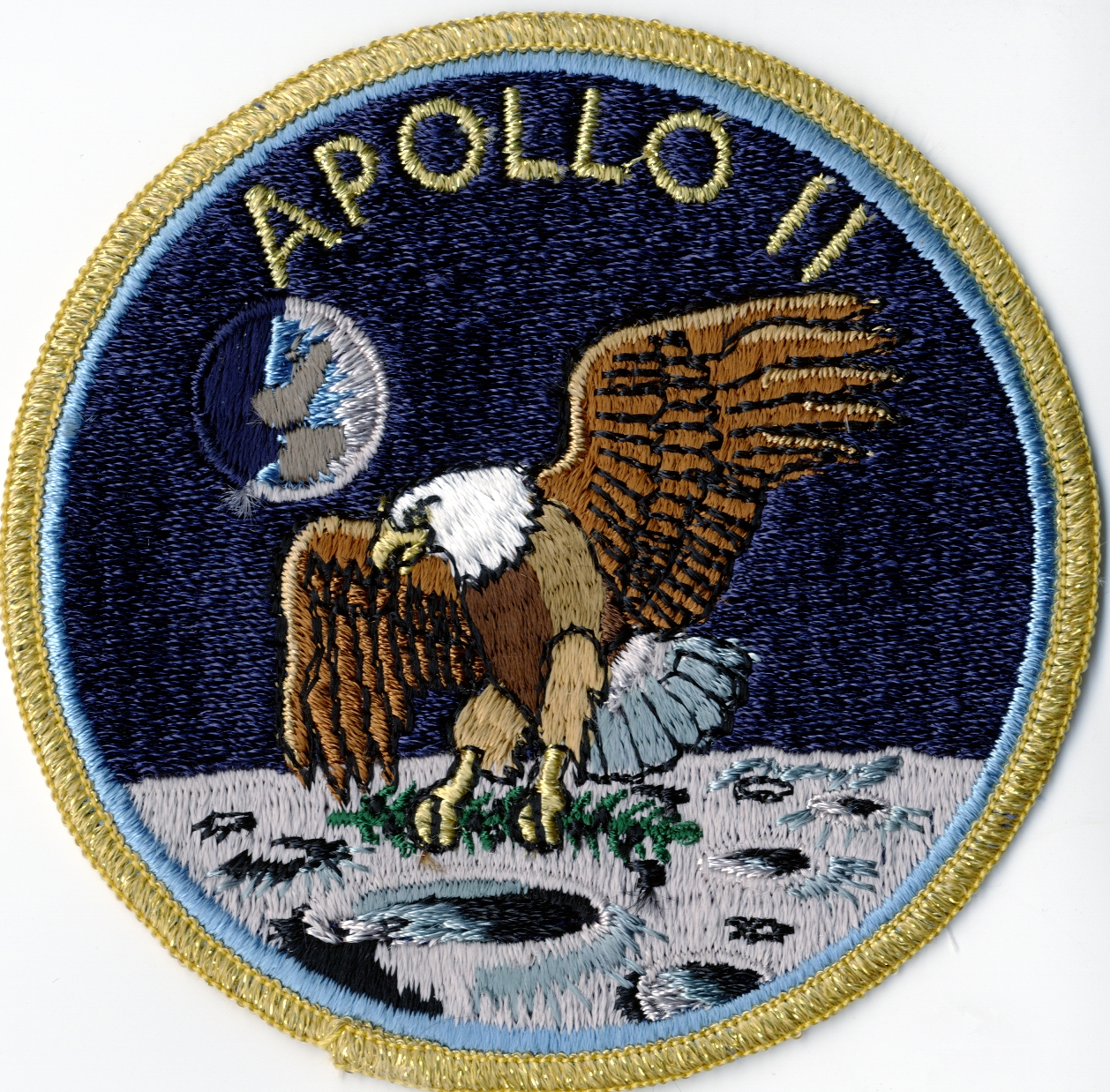